Castables and Masses
Castable Refractory is a kind of refractory material made of granular and powder material, and add a certain amount of binder and moisture together. It has high fluidity, suitable to use castable method construction, no heating can harden unshaped refractory material.
o Rocking Runner and Slag Runner Castables gel bonded
o Low Cement Castables
o High Alumina Castables
o Mortars
o Basic Ramming and Gunning Mass
o Basic Ramming Mass (Induction Furnace)
o Magnesite Ramming Mass (ARC Furnace)
o Basic Gunning Mass
o Tundish Vibro Mass, Tundish Spray Mass
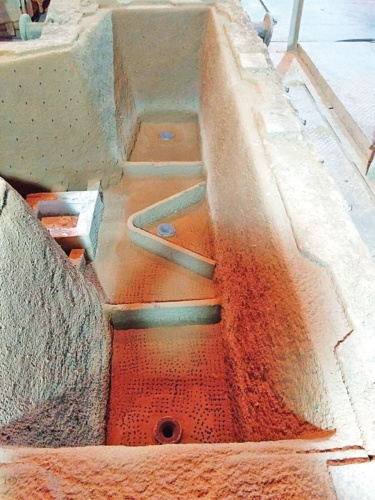
Tundish Working Lining
Low Cement Castables
Low cement castables are new castables with low binder content. The key point is the use of ultrafine particles not exceeding 1 μm. Its thermal shock resistance, slag resistance and erosion resistance are significantly improved, surpassing similar refractory bricks. Further reducing the binder content can produce ultra-low cement castables and cement-free castables.
The product range includes low cement castable of different Alumina content (Al2O3 varying from 45% to 90%) with service range between 1,5000 C to 1,8000 C. These are characterized by Al2O3 content and specific low Fe2O3and low CaO content.
Also water requirement for casting is less than 5%. These castables have very short curing time requirements. These are suitable for use in places where very quick setting is required thus reducing the downtime of Furnaces. These are being extensively used in furnaces like:
o Ladle and Tundish back-up lining
o Sintering Furnace roof
o Soaking pit covers
o Health of re-heating furnaces
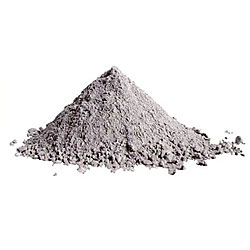
Low Cement Castables
High Alumina Castables
High Alumina Castable is a kind of Refractory Castable which uses High Alumina raw material as aggregates and the powder and then be added with binding agent. High Aluminum Refractory Castable has high mechanical strength, good thermal shock resistance, good corrosion resistance.
The product range includes High Alumina Castables different Alumina content varying from 50% upto 95%. The water requirement of casting is 7 to 10% and have a short curing time. These castables are used in reheating furnaces, steel ladles and as a general purpose repair.
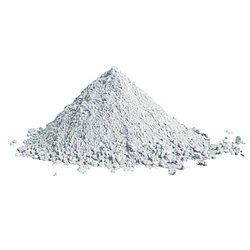
High Alumina Castables
Mortars
Refractory mortar is a specially engineered blend of specific cements, sand, calcium aluminate, cement, and fireclay. It is used to lay firebrick in places that are exposed to extremely high temperature and use in applications such as chimneys, fire pits, barbeques, and pizza ovens.
We manufacture 90K Green Mortar having 90% Aluminum oxide (Al2o3), chemically bonded with excellent bonding strength and resistance to metal penetration.
The properties of 90K Mortar are:
o High strength at higher temperature
o Superior performance in corrosive environments
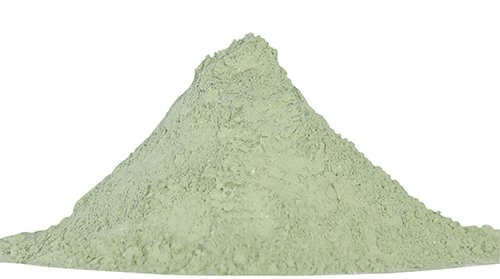
Mortars
Magnesite Ramming Mass
Suitable for Ramming of Electric Arc Furnace, Ultra High Power (UHP), EBT (Eccentric Bottom Tapping) furnaces of various capacities and also as a repair material with quick thermosetting properties.
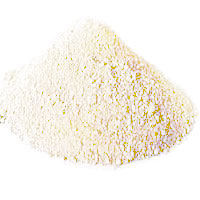
Magnesite Ramming Mass
Basic Gunning Mass
Suitable for Ramming of Electric Arc Furnace, Ultra High Power (UHP), EBT (Eccentric Bottom Tapping) furnaces of various capacities and also as a repair material with quick thermosetting properties.
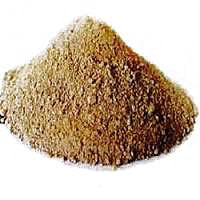
Basic Gunning Mass
Tundish Vibro Mass
o We manufacture magnesite based moldable water-free mix for Tundish lining
o It is easily filled between the permanent layer of Tundish and the steel former
o The forma is heated upto 300<sup>0</sup>C by a hot air generator for 2-2.5 hours, and then removed by crane after cooling
o It is formed at designed thickness. It performs at long sequence lengths more than 20 hours and protects the quality of steel
o Deskulling is a safe and quick process with our vibro mass, reducing downtime and lowering maintenance costs. It can be used in both cold and hot tundish practices
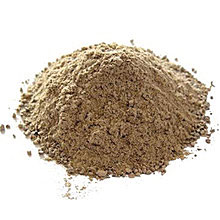
Tundish Vibro Mass
Tundish Spray Mass
The working lining of Tundish plays an important role in providing quality and cost effective steel.
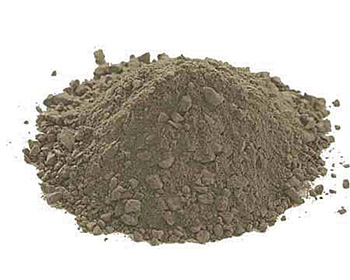
Tundish Spray Mass
TYPICAL FORMULATIONS OF CASTABLES & BASIC MASS | ||||||||||||||
Chemical Analysis (%) | ||||||||||||||
Product | Mortar | High Alumina Castables | Low Cement Castables | Basic Mass | Tundish Vibro Mass | Tundish Spray Mass | ||||||||
Grades | 90 – K Mortar (G) | 60% HA | 70% HA | 90% HA | LC 45 | LC 60 | LC 70 | LC 80 | LC 90 | Gunning Mass | Ramming Mass | |||
Al2 O3 (Min.) % | 90 | 60 | 70 | 70 | 45 | 60 | 70 | 80 | 90 | |||||
MgO (Max.) % | 80 | 84 | 75 | 70 | 80 | |||||||||
Fe2 O3 (Max.) % | 1.5 | 1.5 | 1 | 1 | 1 | 2.5 | 2 | 2 | 2 | |||||
SiO2 (Max.) % | 8 | 5.5 | 15 | 20 | 10 | |||||||||
Cr2O3 % | 2 | |||||||||||||
CaO (Max)% | 4 | 4 | 3.4 | 3 | 3.5 | 3.5 | ||||||||
Physical Properties | ||||||||||||||
Product | Mortar | High Alumina Castables | Low Cement Castables | Ramming Mass | Tundish Vibro Mass | Tundish Spray Mass | ||||||||
B.D. (gm/cc) Min. 1100C/24 hrs | 2.75 | 2.35 | 2.4 | 2.6 | 2.3 | 2.6 | 2.7 | 2.9 | 3.2 | 2.35 | 2.65 | |||
C.C.S. (Kg./cm2) Min. / 1100C | 350 | 750 | 800 | 850 | 700 | 750 | 800 | 850 | 900 | 400 | 450 | 300 | 300 | |
C.C.S. (Kg./cm2) Min. Drying @8000C / 3 hrs soaking | 800 | 850 | 900 | 800 | 800 | 860 | 950 | 1000 | ||||||
C.C.S. (Kg./cm2) Min. Drying @11000C / 3 hrs soaking | 900 | 900 | 950 | 900 | 900 | 950 | 1050 | 1150 | ||||||
C.C.S. (Kg./cm2) Min. Drying @15000C / 3 hrs soaking | 1000 | 1000 | 1000 | 1000 | 1000 | 1000 | 1150 | 1150 | 400 | 70 | 300 | 300 | ||
Thermal Conductivity (k cal/m/hrs0C) | 1.15 | 1.2 | 1.2 | 1.16 | 1.2 | 1.29 | 1.8 | 2.3 | ||||||
P.L.C. max at 15000C | ±1 | -0.8 | -0.7 | ±0.8 | ±1 | -0.8 | -0.7 | ±0.8 | ±0.8 | -1.2 | -1.2 | -3 | -3 | |
Shelf Life (months) | 3 | 3 | 3 | 3 | 3 | 3 | 3 | 3 | 3 | 3 | 3 | 3 | 3 | |
L.B.D. (gm/cc) Min. | 1.6 | 1.7 | ||||||||||||
Skull Removal | Smooth | Smooth | Smooth | |||||||||||
Grain Size (mm) Max. | 6 | 6 | 6 | 6 | 6 | 6 | 6 | 6 | 3 | 5 | 1 | 0.5 | 0.5 |